Condition monitoring of large diameter steel ropes
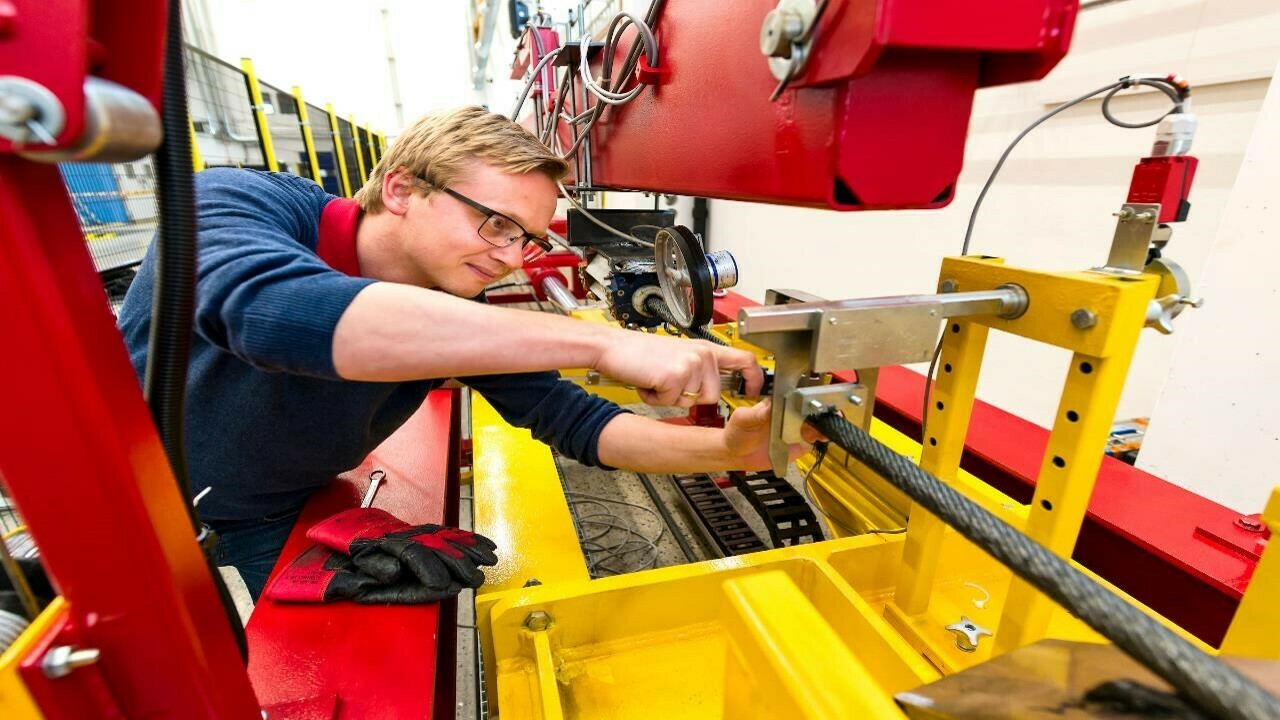
The scope of our work is to benchmark the state of the art monitoring technologies such as the electromagnetic method, acoustic emissions, guided wave ultrasound, eddy current, gamma rays, optical and thermal vision systems and current signature analysis, and develop models for robust diagnostics and prognostics.
Project facts
Name
Condition monitoring of large diameter steel ropes
Status
Duration
04.07.25 - 04.07.25